Category: Blogs
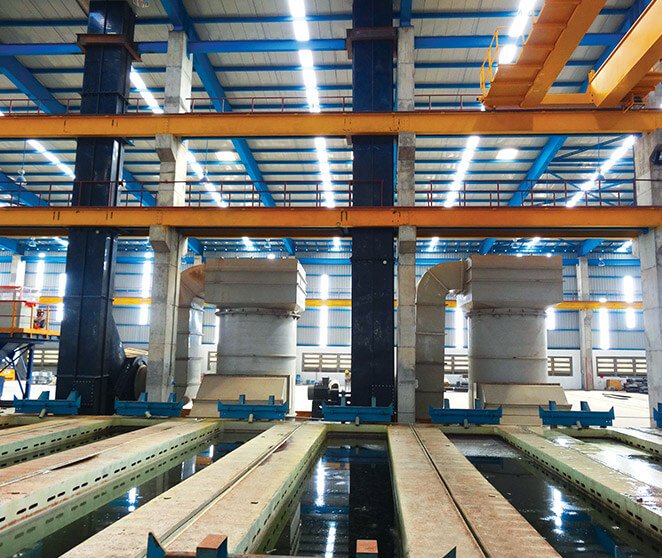
In this era of increased industrialization to meet the requirements and challenges of ever-rising pollution, sustainable development has assumed significance. Rightly so. Pollution control equipment manufacturers are manufacturing a wide range of anti-pollution equipment to reduce pollution and create a healthy environment. In this business-centric blog, we are going to focus on chemical square tank, their role in anti-pollution drive, etc.
Before we take a deep dive into the subject, let’s understand pollution.
Learning about pollution
Pollution impacts the environment, our surroundings, and our lives badly as it leads to loss and destruction of biodiversity, global warming, reduction in the number of plants and animal species, etc. Polluted air and water pose various challenges and threats to human life. Subsequently, it is important to control pollution.
Pollutants
What is a pollutant? Anything that pollutes the environment is called a pollutant. These could be in solid, liquid, or gaseous states. Here is a list of some of the pollutants:
- Acid water
- Coal dust
- Caustic soda
- Cement dust
- Organic waste
- Various oxides
- Inorganic waste pigment
- Smoke & toxic gases
- Acidic gases
- Fly ash
- Pesticides
- Alkalies
The list is endless. Given the ill effects of pollutants on the environment and human beings, it is mandatory to control the emission of pollutants from the source, including factories, manufacturing units, construction sites, etc.
Pollution control equipment
As the name indicates pollution control is a series of scientifically designed equipment manufactured by pollution control equipment manufacturers to control pollution. The objective of this equipment is to prevent a variety of different pollutants from directly entering the atmosphere.
Devices and equipment to control pollution
From the basics, let’s now shift our focus to the core subject, devices, and equipment to control pollution. Pollution control equipments manufacturers are fabricating a wide range of devices to curb the menace of pollution, including a chemical square tank.
- Acid fume extraction system
- White fume extraction system
- Fully enclosed pickling plant
- Furnace fume enclosure
- Wet scrubbing system
- Dust collector filter system
- Bag filters
- Chemical square tank
Benefits of pollution control equipment
Many famous companies are serious about pollution control. Their manufacturing processes are using the latest chemical square tank, to curb the emission of pollutants. Pollution control requires concerted efforts. Mere policy formation and guidelines wouldn’t serve any purpose. Everyone has to come forward to minimize pollution and create a healthy environment to live in.
Here are a few benefits of using the pollution control devices
- Leads to a healthy environment
- Minimizes health hazards
- Health threats to the workforce minimized
- Animals and plants are saved from the ill effect
- Industries become role models for others.
- Nurtures the concept of sustainable development
- Plays a role in making the environment free from pollution
For further information, feel free to connect with a leading pollution control equipment manufacturer. Custom-designed tools and equipment can also be availed from leading manufacturers and suppliers. Your requirement will be analyzed and evaluated. After that team of experts, comprising engineers and technicians will come up with a design and layout. Once approved by the client, this design is converted into equipment.
Conclusion
Together we can make a difference. Sustainable development is the key.
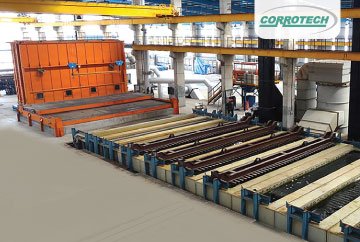
In this manufacturing industry centric blog, we will expand knowledge of readers about pollution control equipment, its benefits and how the equipment’s are helping in saving environment.
The hot dip galvanizing operation has assumed enormous significance in this fast-paced world. Socio-economic development has necessitated its use in numerous ways.
As we move forward, it makes sense to learn the basics about hot dip galvanization. Subsequently, it will be easy to understand the subject.

Learning about hot dip galvanization
Simply put, it is a scientific process of applying a coating of zinc over an iron/steel-made item by immersing it in the molten lava of zinc. As a result, the object becomes robust, durable, and resistant to harsh weather conditions. In a nutshell, the process protects the steel from corrosion.
Pollution during galvanization
During the process of galvanization, effluents are generated from the bathing, washing, and cooling processes. Therefore, it makes sense to use quality-driven pollution control equipment to save the environment from getting polluted. Also, at the same time saves employees working in galvanization factories from hazardous diseases As a result, we human beings can breathe fresh air.
Pollution control device
Leading companies into galvanization employ a wide range of machines, tools, and equipment with the aim to control pollution, and save the environment. A few prominent air pollution control systems deployed in a galvanization setup are:
- Acid fume extraction system
- Whit fume extraction system
- Furnace fume enclosure
Understanding the Acid Fume Extraction System
This mechanized system is designed to absorb the acidic and toxic fumes that generate from the pickling tanks. As a result, toxic fumes are prevented from spreading on the floor. Subsequently, the environment and human health is also saved.
Benefits
You would appreciate the benefits of this brilliant product.
- Minimizes risk to health
- Increases the life of roof structure
- Improved life of cranes and other machines and tools
- Saves environment from unpleasant odor
The quality of the product can be judged from the fact that it is designed for zero discharge and acid neutralization.
White Fume Extraction System
During the process of hot dip galvanization, white fumes get generated when steel/iron-made objects are dipped in the molten lava of zinc. The white fume comprises harmful chlorine and suspended ash particles.
The scientifically designed system helps in the removal of hazardous zinc oxide and ammonium chloride.
Benefits of the machine
Here are the benefits of the environment-friendly product:
- Increased productivity
- Eliminates white fumes
- Improved health of workers
- Creates a safe and healthy environment
Furnace fume enclosure
The brilliant system is designed for the abatement of white fumes that emanate during galvanization. This mechanized enclosure is connected with a dust-collecting cyclone. The latter is again connected with a wet scrubber or bag filter. Here hazardous fumes get cleaned and filtered, before eventually discharging them into the atmosphere.
Benefits
Coming to benefits of this system, it is helpful in the following ways:
- It lowers zinc consumption
- Reduces fuel consumption
- Minimizes health hazards
- Saves workers from health risks
Conclusion
In this era of rapid industrialization, galvanization is the need of the hour. However, a safe environment is also a vital necessity. Accordingly, a sustainable environment is required.
Start exploring the expertise of Arvind Corrotech
Arvind Corrotech is an industry leader offering full-spectrum galvanization solutions. Our quality-driven product range includes Turnkey Hot Dip Galvanizing Plants, Pulse Fired High-Velocity Furnace, Process Tanks, Chemical Storage Tanks, and Pollution Control Equipment.
If you are on the lookout for anything related to quality-driven pollution control equipment, then end your search with Arvind Corrotech. Let’s connect for a mutually beneficial collaboration.
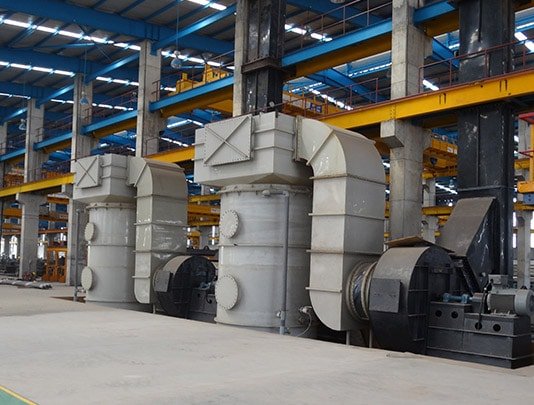
The rising population and its day-to-day needs are giving impetus to industrialization. Industrialization is a boon for socio-economic development, at the same time, it is wreaking havoc on the environment. Subsequently, it leads to pollution. Therefore pollution control machines and tools are important.
A good quality natural environment offers basic requirements to existing, including clean air, water, fertile land for cultivation of crops, and energy among others. Green infrastructure also facilitates in maintaining sustainable development, regulates weather, and prevents natural disasters, like a flood, droughts, earthquakes, etc.
Life can’t be imagined without an environment. A safe and healthy environment is mandatory for the existence of human beings, flora and fauna.
In this blog, we are going to emphasize the benefits of pollution control equipment. In addition to this, our focus will revolve around types of pollution control equipment.
Before we start learning the intricacies of the subject, it’s important to learn the basic definition of the term.
What is pollution control equipment?
In simple words, pollution control equipment is defined as any item, apparatus, or container designed primarily to control air or water pollution. There are numerous types of equipment available in the market. Depending on your industry and the types of pollutants released by your company, you can choose the equipment.
Galvanization industry and pollution
The process of galvanization uses high-tech machines, tools, and technology to apply the coating of zinc on steel/iron-made structures. During the process, harmful fumes, toxic gases, and a host of other pollutants are released. Therefore, it’s imperative to deploy equipment and technology to control pollution. In addition, it is also mandated by local bodies.
Pollution control equipment in galvanization
Galvanization industry-specific pollution control machines and tools have been designed to control pollution during galvanization. The equipment also protects the workforce from numerous health hazards. These include:
- Acid fume extraction system
- White fume extraction system
- Fully enclosed pickling system
- Furnace fume enclosure
- Wet scrubbing system
- Dust collection filter system
Acid fume extraction system
The acid fume extraction system has been designed for the abatement of the toxic fumes that get generated in the pickling tank.
White fume extraction system
It is a specially designed apparatus for the safe abatement of zinc fumes. The system comprises a fume extraction hood, dusty collecting cyclone, a bag filter, etc.
Fully enclosed pickling system
This sophisticated system empowers the users to capture and abate toxic fumes with ease.
Furnace fume enclosure
It is a fixed fume enclosure for preventing the white fumes generated during the galvanization process. Furthermore, the structure controls the spread of fume in the manufacturing area and the open environment.
Wet scrubbing system
Designed using the latest technology, the wet scrubbing system empowers businesses to control air pollution by eliminating the toxic fumes from the exhaust stream. Subsequently, absorbs the fume pollutants.
Dust collection filter system
It sounds like a simple piece of equipment, yet it is a very important piece of equipment. The equipment cleans the air by filtering the dust particles. A bin designed for the collection of the dust, collects the dust, while the filtered fumes exit the cyclone outlet.
Summary
As a responsible citizen, in the interest of the environment, efforts should be made to adhere to pollution control.
Buy the pollution control equipment from Arvind Corrotech
Arvind Corrotech is an industry leader offering full-spectrum galvanization solutions. The company is also a famous manufacturer and supplier of Turnkey Hot Dip Galvanizing Plants. Our quality-driven product range includes Pulse Fired High-Velocity Furnace, Process Tanks, Chemical Storage Tanks, and pollution control equipment.
If you are on the lookout for anything related to pollution control equipment, then end your search with Arvind Corrotech. Let’s connect for a mutually beneficial collaboration.
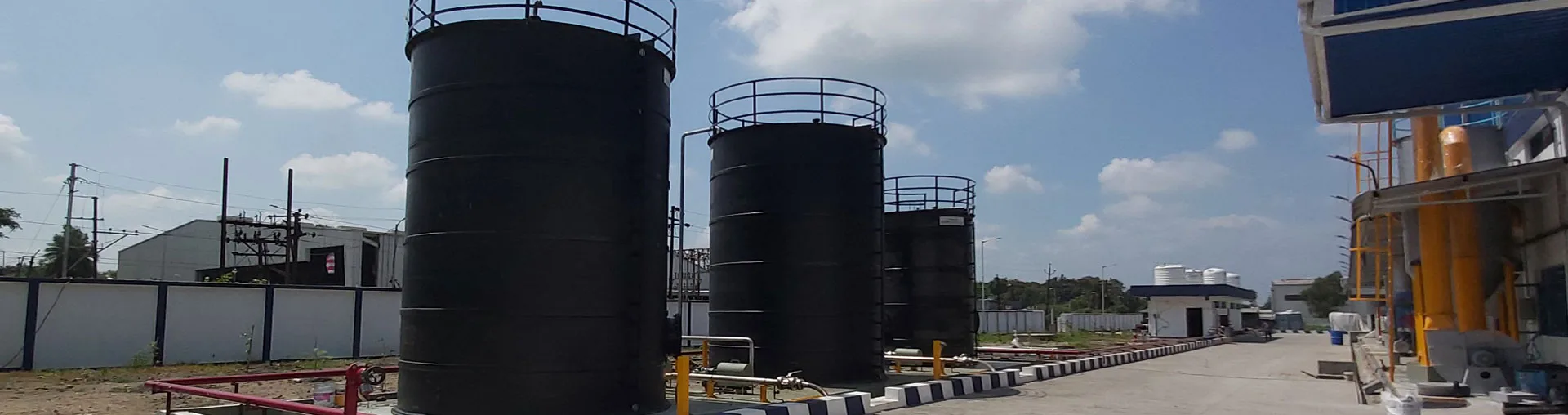
This is a business-centric blog. In this blog, our focus will circum navigate key issues and points related to industrial storage tanks. Before we get into the details andintricacies of the topic, let’s understand the basics.
What is an industrial chemical storage tank?
As the name signifies, industrial chemical storage tanks are employed for storing and safe transport of industrial chemicals. Simply put, these are designed for a wide range of manufacturing and processing industries.
Key objectives of the chemical storage tank
Here are the key objectivesof the chemical storage tank:
- Mixing
- Processing
- Static storage
- Transport of raw chemicals
- Transportfinished chemical products
Material of industrial tanks
Industrial chemical storage tanks are manufactured using various types of material. Its use fundamentally depends on the type of material to be stored.
- HDPE storage tank
- FRP (fiber reinforced plastic) tanks
- Steel and high alloy tanks
Chemical storage tank manufacturers, for instance, Arvind Corrotech adhere to industry standards to deliver excellence-driven storage tanks.
List of industrial chemicals stored in chemical tanks
The specially designed storage tanks for chemicals are suitable to safely store the following chemicals:
- Propane
- Liquefied natural gas (LNG)
- Fertilizers
- Petroleum products (gasoline, diesel, petrol, etc.)
- Crude oil
- Sulphuric Acid (H2SO4)
- Ethylene
In addition to the above chemicals,many other industrial chemicals are stored in industrial tanks, Sodium Hydroxide, Propylene, and Nitrogen. For the unawares, over 150 million tons of Ethylene (C2H4) is produced annually for various purposes.
Salient features of storage tanks
Now let’s shift our focuson the salientfeatures of the tanks. Here are the salient features:
- Sturdy
- V. stabilized
- Durable & long-lasting
- Withstands harsh weather environments
- Leak-proof
- Resistant to chemicals
- Resistant to corrosion
Tanks in different shapes
Storage tanks for chemicals in different shapes are availablein the market. Depending on their industry and needs, industrialists can choose the design and shape. Here are a few common designs:
- Vertical storage tanks
- Horizontal tanks
- Square storage tanks
Industries using chemical tanks
In this blog, we have covered a few crucial subjects with the objective to expand the knowledge of readers and professionals working in different manufacturing industries. Now, the most important question arises. Which all industries use chemical tanks? Here is the list of industries using storage tanks:
- Textile
- Petrochemicals
- Chemicals
- Colours and Dye
- Galvanization
- Steel
- Tyre
- Plastic
- Paper
Capacity
The chemical storage tanks are available in different capacities. Their common capacities in litres include 500, 1000, 1500, 2000, 3000, 4000, 5000, 10,000, etc.
For a specific shape and size, you can connect straight away with the leading manufacturers and suppliers. There are a few who are experts in customization.
Conclusion
Every material has its properties. It is suitable for a few specific chemicals. Every tank can’t store any kind of chemical. You are advised to make a proper inquiry while procuring a tank for your industry. Buy the tank which is suitable for your industry.Never take a decision in haste since it may have wide spread implications.
Join hands with Arvind Corrotech
Arvind Corrotech is leading Hot Dip Galvanizing Plant Manufacturer, offering full-spectrum galvanization solutions. Our quality-driven product range includes Turnkey Hot Dip Galvanizing Plants, Pulse Fired High-Velocity Furnace, Process Tanks, Chemical Storage Tanks, and Pollution Control Equipment.
If you are on the lookout for anything related to repair and modification services for process tanks and galvanizing plants, then end your search with Arvind Corrotech. Let’s connect for a mutually beneficial collaboration.
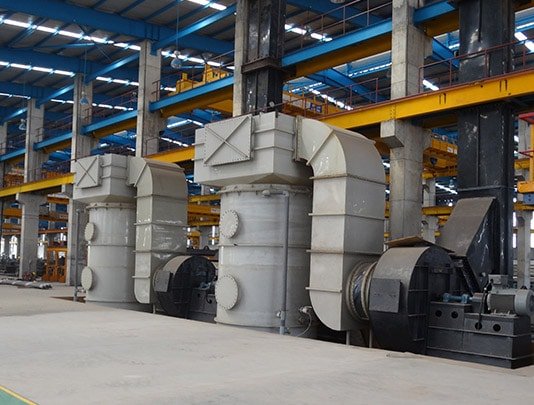
In this era of ever-rising socio-economic growth, the manufacturing and infrastructure sector are showing consistent growth, riding on demand and supply theory. Rapid growth in the various manufacturing sector, for example, cement, chemical, textile, leather, plastic, tyre, etc. to overcome the demand and supply challenges. At the same time, effluents that discharge from the plants and factories wreak havoc on the environment, leading to environmental pollution. Keeping these factors in view and saving the environment from pollution, the use of pollution control equipments becomes a necessity.
Our focus in this blog will remain on a few critical subjects that have a direct or indirect impact on the environment. In order to save the environment and push sustainable development, filtration systems for pollution control are getting prominence these days. And why not?
Benefits of pollution control and filtration plants
- Prevention is the key to preserving wetland, groundwater resources, human health, and sustainable development
- Prevents the environment by conserving natural resources
- Pushes inclination towards sustainable development
- Protects human beings from health hazards, like bronchitis, heart disease, lung cancer, etc.
- Compliance with local regulations empowers your business to operate without any apprehension
Pollution control equipments
Any machine or tool or equipment that helps control pollution falls under the category of pollution control machines and tools. In this section, our focus will remain on tools and pieces of machinery widely used to combat pollution. Here are a few major equipments:
- Acid fume extraction system
- White fume extraction system
- Pickling plant
- Furnace fume enclosure
- Wet scrubbing system
- Dust collector filter system
- Bag filters
- Filtration systems
These equipments are designed to remove hazardous particles and pollutants, like sulfuric gases, fumes, pollutants, odors, and vapors. Harmful impacts like acid rain, smog, carbon emission, etc. are the result of these pollutants. Threats to the environment and the subsequent impact on health are manageable issues.
Integrated approach
Integrated pollution control is a comprehensive approach that aims to prevent and minimize pollution and human lives. It is the need of the hour in today’s era wherein focus remains on striking balance between industrial growth and safety of human lives. Countries across the globe are incorporating the integrated approach to control pollution in their manufacturing and infrastructure development processes.
Filtration systems for pollution control
This is an important system, in place in numerous manufacturing units and factories. For example galvanization plants, cement manufacturing, paper manufacturing factories, etc. It has been used extensively for various benefits, including to control pollution and shield the health of the workforce.
Main objective
The key objectives of the system include:
- Reduction of hazardous substances
- Recycling
- Treatment
- Final disposal
Major components of the system
- Dust collection system
- Vacuum systems
- Wet scrubbers
- Welding exhaust systems
- Fume extraction arms
- Oil mist collectors
- Dust control booths
- Source capture hoods
- Downdraft tables and benches
- Air filter housings
- Dust collector filters
Join hands with Arvind Corrotech
Arvind Corrotech is an industry leader offering full-spectrum galvanization solutions. Our quality-driven product range includes Turnkey Hot Dip Galvanizing Plants, Pulse Fired High-Velocity Furnace, Process Tanks, Chemical Storage Tanks, and Pollution Control Equipment.
If you are on the lookout for anything related to pollution control equipment, then end your search with Arvind Corrotech.
Let’s connect for a mutually beneficial collaboration.

Over the years technology and innovation have helped a wide range of industries in furthering their evolution. Even the process of galvanization has also been benefitted from the emergence of technology. Corrosion technology is no more the same, it used to be in the past. Continued innovation is paving the way for new processes and methods of galvanization.
In this short and meticulous blog, we are going to focus on galvanization, its benefits and advantages, and a host of other significant issues.
Learning about the galvanization
Dear Readers, at the outset, let’s understand the term galvanization in simple words before we take a deep dive into the all-important subject.
Rust is the biggest opponent of iron and other metals. Overexposure of metallic parts to inclement weather, scorching heat, saline water, etc. leads to corrosion. Corrosion impacts the life of the metal.
Galvanization is one most reliable methods to prevent iron and steel metal from corrosion. There are various types of methods available for protecting the metal from corrosion.
How does it happen
Under the process of galvanization, a thin layer of zinc coating develops on the base metal, when it is dipped in the lava of molten zinc. The zinc layer develops on the metal during the process. It helps prevent metal, like iron and steel from corrosion through a protected shield. This layer of zinc though as thin as the thickness of a photocopy paper helps the metal withstand inclement weather.
The hot dip galvanizing process generates white fumes when steel is dipped in the molten zinc. The fumes that emanate are extremely hazardous due to the presence of chlorine and suspended ash particles. If inhaled, it may also be considered harmful for health. Also, they deteriorate the overhead cranes and the shed life. Hence, it becomes apparent to establish a system for fume abatement and discharge. This entire system is known as Zinc Fume Extraction System,
Hot dip galvanizing is one of the most sought-after methods for the galvanization process of metal across industries and geography.
Galvanizing benefits
Galvanizing is all-around. It wouldn’t be an exaggeration if we say the process has become an integral part of our life. Life can’t be imagined without galvanization. In this section, we are going to talk about the core of this blog.
Industrial use
Owing to the amazing benefits of galvanization, it has found usage in a wide range of industries. Industries like automobile, Infrastructure development, wind energy, transport- shipping, railways, airplane, etc., and sports to name a few are using the innovation for their benefits. Numerous strictures across the globe are using galvanized steel for its amazing properties. These types of metal have the properties to counter and withstand inclement weather, resulting in optimized durability. Anti-corrosion properties of the zinc layer are the biggest instrument of the galvanization process.
Join hands with Arvind Corrotech
Arvind Corrotech is an industry leader offering full-spectrum galvanization solutions. Our quality-driven product range includes Turnkey Hot Dip Galvanizing Plants, Pulse Fired High-Velocity Furnace, Process Tanks, Chemical Storage Tanks, and Pollution Control Equipment.
If you are on the lookout for anything related to galvanization, then end your search with Arvind Corrotech.
Let’s connect for a mutually beneficial collaboration.
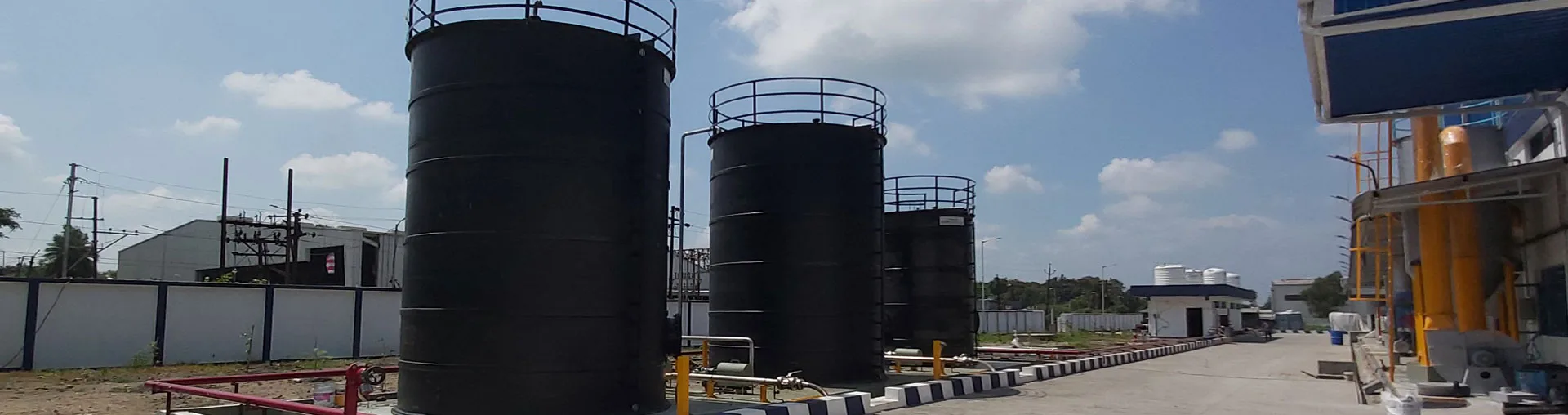
This isn’t a conventional subject for our readers, yet, it has great significance for everyone. Directly or indirectly, chemical tanks are touching our lives. For those who are working or associated with the textile, chemical, petrochemical, food and beverage, and pharmaceutical industries, this is going to be an interesting subject. This will further expand their knowledge base about the subject. For students and research scholars, this is going to present a wide range of facts and figures enabling them to prepare their reports and assignments.
What is a chemical tank?
Before heading towards the intricacies of the subject, it’s important to learn the term in simple language. A chemical tank is a sophisticated storage container to store a wide array of chemicals that are in use in numerous industries, including pulp and paper. The sophisticated tanks are available in numerous sizes and standard shapes. Depending on chemical and fluid, chemical tank manufacturers across India fabricate these sophisticated tanks.
Why are we using the word sophisticated though it’s only a tank? The tank looks ordinary in design, a cylindrical structure, but this kind of tank is for special chemicals. These chemicals are hazardous in nature, may lead to disaster and environmental consequences, if not stored with adequate measures. While purchasing the tank for your manufacturing process, don’t forget to ask for features from the chemical tank manufacturer.
Purpose of chemical tanks
What is the purpose of a chemical tank? Is it only for storing? Calling the tank a storage tank delimits its benefits and industrial applications. It has numerous uses, including:
- Storage of industrial chemicals and fluids
- Chemical process
- Mixing of chemicals for a wide array of processes
- Transportation of finished products
- Transportation of raw material
A picture is crystal clear now. A chemical tank is a versatile container with numerous uses as mentioned above.
Types
Tanks are of different types. These are identified with the type of chemicals they hold.
- Acid tanks
- Holding tanks
- Feed tanks
- Blend and mix tanks
- Pressure vessels
- Buffer tanks
- Pump tanks
- Reactors
- Receiver tanks
- Filtrate tanks
- Stripper/Scrubber Columns
- Surge tanks
- Weighing vessels
- Jacketed tanks
- Solution tanks
- Solvent tanks
- Storage tanks
- Circulation tanks
Over the years, demand for chemical storage tanks has increased substantially. Storing chemicals is a challenging task. An ideal industrial chemical storage tank offers a financial and business advantage, as a businessman and a professional heading a company that’s what you require and expect from a chemical tank and chemical tank manufacturer.
Material and chemical
A chemical tank is designed to store a few selected chemicals only. Every tank has its specification and features. Since hazardous, industrial chemicals should be stored according to the standard instruction. You can take guidance from a chemical tank manufacturer.
- Hydrochloric acid
- Sodium hypochlorite
- Sodium hydroxide
- Ferric chloride
- Soda ash sodium carbonate
- Industrial wastewater
- Sulfuric acid
- Urea exhaust
- Petrochemical exhaust
Chemical storage tank manufacturers across India, including Ahmedabad, are constantly working towards using the latest technology and innovation to enhance the quality of the tank.
The current market scenario and impact of the corona pandemic
According to industry experts, the industry is heading towards a positive growth trajectory with increasing opportunities in the petrochemical, food, and beverages, and pulp and paper industries. The corona-induced pandemic havoc is affecting the growth of the market. The global chemical storage tank market will recover from the havoc in the current FY 2021 and it is poised for substantial growth, it is expected to reach an estimated $5.3 billion by 2025.
Buy from an expert only
As mentioned in the blog earlier, quality matters. Buy product from a leading chemical tank manufacturer only with a proven track record.

ore making a deep dive into the important subject, its definition assumes significance here. Learning would be much simpler then. The blog is going to focus on the definition and benefits of the process that has been transforming our day-to-day lives. Many of us may not be aware. However, we all come across galvanized items almost every day.
Learning about the term
Hence, what is this process all about? Why can’t we make an endeavor to tell our readers and those associated with the industry in layman’s language? Galvanizing is the process of applying a protective zinc coating or layer to steel or iron. The objective behind the process is to protect the iron metal from corrosion. The process makes the metal rust-proof!
Since the Hot dip galvanizing process offers numerous benefits, it has been used in numerous industrial applications. Its versatility makes it favourite among many industries using an iron-on large scale for a wide range of processes.
Why only Zinc?
Why do most of the galvanizing processes rely on zinc across the globe? This question assumes significance in the context of this significant article. There are obvious reasons behind choosing zinc over others. Here are a few features that make the zinc stand out from the rest:
- The corrosion of zinc is very slow
- Durable
- Provides cathodic protection
- Even corners and smaller areas get protected
Machinery and tools for the process
The process of galvanizing is carried out through tried and tested machinery and tools. Industry experts are of the opinion that machines play an important role during the process. For example, surface treatment tanks, acid room enclosure, chemical pump, dry unit, galvanizing furnace and kettle, heat exchanger, waste gas washing system, baghouse filter, helping equipment, loading, and offloading equipment, conveyor systems, transfer car, and a host of others.
The machines’ terminology may vary from company to company. However, more or less, these are the same.
The benefits of using galvanization
The various reasons support the exponential rise of the use of galvanization. These are:
Affordable and reliable
- Lower cost
- Minimum maintenance
- Prolongs the life of the coated metal
- Provides exceptional resistance to mechanical wear and tear of the metal made items
- Even minor areas get protected
- Saves precious time of painting the metal made space
- Saves money needed for replacing the corroded metallic items
Industries using galvanization
The hot-dip galvanizing process has found application in countless industries and sectors. These include:
- Wind and solar industries
- Automotive industry
- Construction industry
- Energy industry
- Telecommunication industry
From a galvanizing process perspective, the hot dip galvanizing process is predominantly a two-step process:
First step: Preparation of the metal/ steel for the process
Second step: Immersing the metal in a bath of molten zinc
First step: Preparation of the metal/ steel for the process
The sophisticated scientific process begins by executing the preparation of steel/ iron to accommodate zinc coating. It takes place through pickling. The metal piece goes through washing in an alkaline solution. Through this process rust, grease, and similar impurities get removed.
Second step:
The second step comprises numerous processes and stages to form the zinc coating over the metal. Subsequently, the metal is immersed in a bath of molten zinc. Also, different parameters must match.
Our focus is to increase the knowledge of readers through the basic information about the process. Readers, we will share more information about the key subject in future blogs. Keep watching this space. In the future, we are going to write on many relevant topics for readers. Here is an example, why galvanize plants?
Where to buy the machine?
If you are looking for a hot dip galvanizing plant, don’t forget to explore Ahmedabad, Gujarat! The leading economic hub has a few companies. These companies have the expertise to offer complete Hot dip galvanizing process solutions!

Manufacturing units and chemical companies use a wide range of tanks for various applications. Applications include surface treatment processes and storage tanks. Furthermore, these tanks are available in different types and configurations and play a significant role. These tanks store intermediate, semi-finished, and final products. Besides, the tanks are also used to complete many important processes.
In this short and important write-up, we are focusing on the role and application of tanks. Besides, industries using the product will remain our important priority.
Different types of tanks
The design, construction, and operation of tanks require experience and expertise. Besides, crucial subjects like chemical and acid compatibility with tank material, leaks, spills, loading, and unloading also present various challenges and environmental threats.
There are several types of tanks, depending on their applications.
- Chemical process tanks
- Storage tanks for industrial chemicals
Chemical process tanks
Tanks for chemical/ surface treatment processes require brilliant design and construction as the tank comes across numerous challenges. Moreover, such tanks undergo various tests and experiments to ensure their competency to withstand chemical and physical challenges. All worst-case scenarios are visualized, created, and experimented with to finalize the design and ensure quality.
Material
These tanks are completely different from normal tanks. In addition, special-purpose tanks use HDPE, & PP (non-metallic) among others to manufacture.
Why do industries use specific tanks?
Industrial tanks perform a wide range of applications and are suitable for use where MS tanks do not work. Arvind Corrotech is a leading company with a modern manufacturing facility in Ahmedabad, India. It offers a wide range of excellence-driven Chemical Tanks.
Types
- Acid tanks
- Blend and mix tanks
- Buffer tanks
- Circulation tanks
- Feed tanks
- Filtrate tanks
- Holding tanks
- Jacketed tanks
- Pressure vessels
- Pump tanks
- Reactors
- Receiver tanks
- Solution tanks
- Solvent tanks
- Storage tanks
- Stripper/Scrubber Columns
- Surge tanks
Similarly, there are many other uses of tanks. Application
Chemical process tanks have found applications in plenty of industries. These include:
- Textile
- Leather
- Paper
- Plastic
- Steel
- Oil and petrochemicals
Harsh challenges
The process tanks witness harsh chemical and manufacturing processes. Therefore, they should be resistant to corrosion and harsh weather, for example, rainfall and cyclone.
Chemical storage tanks
As a businessman, if you plan to procure a chemical storage tank for your manufacturing process, it’s important to the chemical you are planning to store. Here is a classic example of a lack of knowledge. Many think that a tank that stores water and other edible fluids is competent to hold industrial chemicals. This is a wrong perception. Therefore, it’s important to buy the right product. And a tank is a tank? This is not true always!
Why do industries require special tanks?
A chemical storage tank has various uses, for instance, storage, mix, and transport of a wide range of chemicals. You might have seen similar tanks at chemical factories, surface treatment plants, pharmaceutical companies, textile factories, etc.
Different materials for different chemical
A few chemicals require a different type of material for storage. Let’s understand it with an example, highly oxidizing materials, including sulfuric acid. It can’t be stored in a normal tank as oxidation degrades the tank. It can cause a dangerous situation. Experts are of the opinion that to store such chemicals, special-purpose materials i.e. PP, and HDPE is a must.
Why tanks are necessary?
Don’t forget that chemicals that produce sludge, including ferric, alum, and polymer offer many challenges. The sludge-producing chemicals require tanks with a few specific features. It should drain completely. The fuming tanks require bottom full drainage. Why is it like that? There’s a logical reason behind this. A similar kind of design doesn’t require a person to enter the tank for cleaning.
Storage of different chemicals
These special signed tanks store several types of hazardous industrial chemicals, these include below mentioned few among others:
- Hydrochloric acid
- Sodium hypochlorite
- Sodium hydroxide
- Sulfuric acid
- Urea exhaust
- Petrochemical exhaust
- Ferric chloride
- Soda ash sodium carbonate
- Industrial wastewater
Choose the perfect manufacturer
As chemical processes require specific chemicals, never compromise with quality. The name and fame of the manufacturer are important. Few manufacturers in Ahmedabad with rich experience in manufacturing chemical process tanks and chemical storage tanks have hands-on experience.