Category: Galvanizing Plant
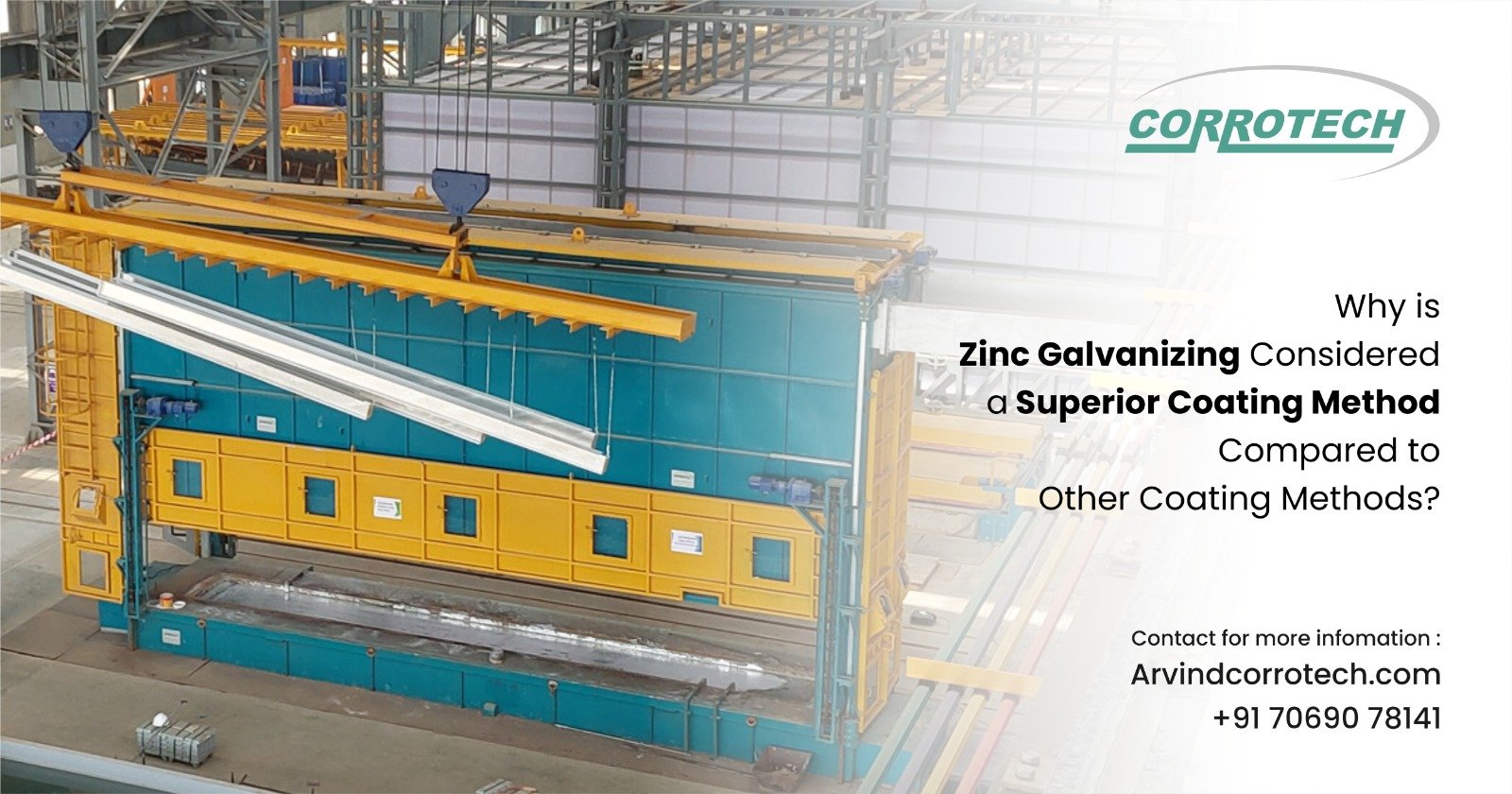
It turns out that corrosion protection is a critical consideration when discussing metal surfaces. There are several metal coating techniques in the market, and each has certain benefits and some disadvantages of its own. However, due to a number of advantages like strong protection and affordability, zinc galvanizing has become a popular option recently. However, still many industries continue to employ traditional methods like painting, powder coating, electroplating, and many others. This article will explain why zinc galvanizing is ideal for your needs by contrasting various zinc galvanizing with various coating techniques utilized in the business.
The zinc galvanizing process
The metal is submerged in molten zinc during the zinc galvanizing process to produce a tough coating that resists corrosion. A wide range of sectors, such as infrastructure, automotive, and construction, heavily depend on the zinc galvanizing process. The extended corrosion resistance that the zinc galvanizing process provides is one of its most significant benefits. The edges and fissures that are challenging to coat completely with conventional coating procedures are certain to be covered when the metal is dipped into the molten zinc. The little maintenance required is an additional remarkable advantage that is important to consider.
We will now go deeper into understanding different coating methods and understanding why the process of zinc galvanizing stands out.
- Painting as an alternative coating method
Painting is one of the earliest techniques for preserving metal objects; it entails putting a liquid coating on the metal that eventually dries up to produce a protective surface. Because painting needs to be done frequently and repainted to maintain its protective characteristics, it may be a time-consuming process in big production enterprises. In abrasive conditions, paint can readily flake, peel, and wear off, which over time can cause metal to corrode.
When we compare the painting method with the zinc galvanizing method it is less durable, time consuming and requires frequent maintenance which makes it unsuitable for industries with higher output rates.
- Powder coating
Powder coating is another popular method which involves the use of dry powder which is electrostatically charged and then treated with heat to form a protective layer from corrosion. Despite a few advantages, powder coating methods have their own set of disadvantages like being more expensive in the initial phases. The second disadvantage can be that it requires a thorough surface preparation, before the process which makes it time consuming and maintaining the exact thickness of the coating on the entire surface can be the biggest challenge.
When compared with zinc galvanizing, powder coating fails in providing long term corrosion protection and it can also fail in providing superior aesthetics because of the uneven coating layers.
- The electroplating process
The process of electroplating uses an electrical current to deposit a thin layer on the surface of the metal to protect it from corrosion. The method delivers smooth coating but is not preferred more because it involves dealing with hazardous chemicals which requires proper disposal. Also the method of electroplating fails to provide complete protection to complex shapes and can prove to be more expensive.
When compared with zinc galvanizing, electroplating turns out to be more expensive because of the complexity of its process and also lacks the robust protection offered by zinc galvanizing plants.
Why is Zinc Galvanizing Superior?
After going through the various coating methods, we have made it very clear that the zinc galvanizing process has a number of benefits attached to it, making it the best choice for metal surfaces. Complete coverage, strong adhesion, environmental benefits, cost-effectiveness, minimal maintenance are some of the factors which greatly contribute to the superiority of the process. We can conclude that when compared to all the other coating methods, zinc galvanizing stands out to be the most reliable and durable process of corrosion protection.
We at Arvind Corrotech, specialize in zinc galvanizing plant operations and even assist you with the complete galvanizing plant setup. Our commitment to quality and great experience in this field will make sure that through our galvanizing machines you receive the best protection for all your metal surfaces and products.
By choosing a zinc galvanizing plant, you are making a great investment which will help you save the most in your future.
For more information on the benefits of zinc galvanizing process, contact our team of experts today!

In the industrial landscape of Gujarat, where manufacturing and infrastructure projects thrive, corrosion protection is paramount for ensuring the longevity and durability of metal components and structures. Galvanizing, a process of applying a protective zinc coating to steel or iron, is a widely used method to prevent corrosion and extend the lifespan of metal products. In Gujarat, several galvanizing plants stand out as leaders in providing high-quality galvanizing services to various industries. Let’s explore why these plants are considered premier providers of corrosion protection and how they contribute to the infrastructure and industrial development of the region.
Cutting-Edge Galvanizing Technology
At the core of premier galvanizing plants in Gujarat lies cutting-edge galvanizing technology aimed at delivering superior corrosion protection and surface finishing. These plants are equipped with state-of-the-art galvanizing lines, featuring advanced pre-treatment, dipping, and post-treatment processes to ensure uniform coating thickness, adhesion, and coverage on metal substrates. With automated systems, precise temperature control, and strict quality assurance measures, they achieve optimal galvanizing results that meet or exceed industry standards. By leveraging innovative technology and best practices, premier galvanizing plants in Gujarat provide customers with durable and reliable corrosion protection solutions for their metal products.
Comprehensive Galvanizing Services
Premier galvanizing plants in Gujarat offer a comprehensive range of galvanizing services to cater to the diverse needs of industries such as construction, infrastructure, automotive, agriculture, and manufacturing. Whether it’s small components, structural steel beams, or large fabrications, these plants have the capability to galvanize a wide variety of metal products, regardless of size, shape, or complexity. Services may include hot-dip galvanizing, centrifuge galvanizing, and powder coating, as well as custom solutions such as duplex coating for enhanced corrosion resistance in aggressive environments. With their extensive expertise and versatile capabilities, premier galvanizing plants in Gujarat provide customers with cost-effective and reliable corrosion protection solutions tailored to their specific requirements.
Stringent Quality Control and Compliance
Quality control is of utmost importance in the galvanizing process, and premier plants in Gujarat adhere to stringent quality control measures to ensure the integrity and performance of their coatings. They conduct thorough inspections and testing at every stage of the galvanizing process, from surface preparation and fluxing to zinc coating and finishing, to verify compliance with industry standards and customer specifications. Additionally, they invest in modern laboratory facilities equipped with testing equipment for measuring coating thickness, adhesion, and corrosion resistance, as well as conducting salt spray and accelerated weathering tests. By prioritizing quality control and compliance, premier galvanizing plants in Gujarat deliver coatings of the highest quality and durability, earning the trust and confidence of their customers.
Commitment to Environmental Sustainability
In addition to providing quality galvanizing services, premier plants in Gujarat are committed to environmental sustainability and responsible business practices. They implement environmentally friendly processes and technologies to minimize the environmental impact of their operations, such as recycling wastewater, capturing and reusing zinc dross, and implementing energy-efficient practices. Furthermore, they comply with regulatory requirements and industry standards for environmental protection, ensuring that their operations are conducted in a manner that preserves natural resources and minimizes pollution. By prioritizing environmental sustainability, premier galvanizing plants in Gujarat contribute to the region’s economic development while safeguarding the environment for future generations.
Customer-Centric Approach and Timely Delivery
Premier galvanizing plants in Gujarat are known for their customer-centric approach and commitment to delivering high-quality services in a timely manner. They prioritize customer satisfaction and strive to exceed expectations by providing personalized attention, responsive communication, and efficient project management. Whether it’s accommodating tight deadlines, coordinating logistics, or offering technical support and guidance, these plants go the extra mile to ensure a positive experience for their customers. With their focus on reliability, professionalism, and customer service excellence, premier galvanizing plants in Gujarat are trusted partners for industries seeking corrosion protection solutions that meet their needs and exceed their expectations.
Conclusion:
In the dynamic industrial landscape of Gujarat, premier galvanizing plants play a crucial role in providing corrosion protection solutions that safeguard the durability and longevity of metal products and structures. With their cutting-edge technology, comprehensive services, stringent quality control, commitment to environmental sustainability, and customer-centric approach, these plants uphold the highest standards of excellence in galvanizing. Whether it’s protecting infrastructure, enhancing manufacturing efficiency, or ensuring the reliability of agricultural equipment, premier galvanizing plants in Gujarat are trusted partners for industries seeking corrosion protection solutions that deliver durability, reliability, and peace of mind.

The automatic systems for the galvanizing plant are no longer an opportunity for showoff. It is a necessity to maintain the viability of the business and cut down numerous needless expenses.
The picture is clear, in this blog, we are going to highlight the significance of galvanizing plant automation solutions for industry and its many benefits. However, before that happens and we take a deep dive into the subject, it makes sense to learn about the galvanization process.

Learning about the hot dip galvanization process
Hot dip galvanizing is a globally famous methodology wherein iron or steel-made items are immersed in molten zinc lava. Afterward, a metallurgical reaction occurs between iron objects and zinc. Subsequently, a layer of zinc coating occurs. This coating lends amazing features to the metal, it becomes resistant to corrosion and harsh weather conditions.
Machines and tools
The hot-dip galvanizing process is a highly sophisticated scientific process involving high-end machines, tools, and technology. The automatic systems for galvanizing plants provide several benefits for the galvanizing industry. As an owner of an industry or someone occupying a senior position, you look for processes that are lean and mean, at the same time facilitating flawless functioning of the plant.
Benefits of the galvanizing plant automation solutions
Here are the benefits of automation of galvanization plants. This section would be an eye-opener for many, especially those working in the industry.
Flawlessly operation of the plant
The Fully automatic solution helps in the seamless operation of the plant. Thereby, helping you to implement lean management, easily calculate return on investment, and identify bottlenecks, if any. Eventually, it leads to maximum efficiency.
Reduces manpower
A typical galvanization plant is labor intensive. However, with the use of galvanizing plant automation solutions, you can eliminate unnecessary manpower costs, increasing overhead costs. Reduced manpower means additional savings and revenue generation. This is a scenario many of you have aspired for.
High-end electrical control panels
With automation comes high-end electrical control panels, fabricated using the latest technology. As a result, you and your staff are empowered to control and manage the plant with ease. You can easily trace different cables spread across the plant.
Plant supervisory control systems
High-end automatic systems for galvanizing plants allows the industry decision-maker to continuously monitor plant functioning, operation, and performance. Therefore, you have the power to evaluate processes dynamically. At the same time, you can identify various bottlenecks. Timely identification and immediate solution reduce any kind of operational flaw.
Process control and monitoring
This is again a vital part of automatic systems for the galvanizing plant. In this era of ruthless market competition, this kind of solution assumes massive significance. These modern technology-driven systems measure and monitor various plant processes and production systems. Consequently, send reports to supervision systems, including control panels and MES.
Remote access and control systems
The modern system is an integral part of galvanizing plant automation solutions. It comprises PLC-based technology and is further combined with router and HMI. It helps to interact with different equipment and plant parts and gather key information.
The system has the competency to monitor all the required parameters and indicators. Furthermore, it sends necessary alerts in case of maintenance or malfunction. As a result, it allows the top management/ engineers to make instant and dynamic decisions.
Plant safety
The automatic systems for the galvanizing plant are safe to use and must in this era driven by competition. It eventually helps you scale your business.
Conclusion
Considering its impact and benefits in hot dip galvanizing plants set up, it is highly recommended by industry experts.
If you are looking for galvanizing plant automation solutions, then end your search with Arvind Corrotech.

In this business-centric blog, we will emphasize an extremely important subject, galvanizing plants. A wide range of issues will be covered ranging from basic definitions to benefits of the industrial process.
Before we take a deep dive into the industrial subject, let’s make an effort to understand the industrial term which is our defining socio-economic life.
Learning about galvanization
What is galvanization? For many of you, it is a new term. Galvanization is a scientific process wherein a thin layer of zinc metal is applied to iron/steel-made objects to prevent them from corrosion.
Hot-dip galvanizing plant
According to experts, the most common method for galvanization is hot-dip galvanizing. Under this popular process, steel sections are dipped in a bath of molten zinc. The zinc layer acts as a shield and protects the metal from corrosion and in turn, increases its durability many times. Hot-dip galvanizing plants in Ahmedabad are tailor-made for the purpose. Galvanizing plant manufacturers are using the latest machines and tools to manufacture an excellent plant.
The three steps of the hot dip galvanizing plant
The hot dip galvanizing process comprises three major steps:
- Surface preparation
- Galvanizing
- Inspection
How does the zinc layer protect iron structures?
There is a scientific reason. As zinc metal is hyperreactive, it reacts with air to form a hard layer of zinc oxide on the metallic structure. This layer works as a protective shield and prevents air from passing through it. Subsequently, protecting the iron/ steel from corrosion.
From basics, let’s now shift our focus to important reasons why industries galvanize steel?
Durable: Galvanization has been transforming many industries with its incredible feature. It multiplies the durability of the product many times.
A worthwhile investment: Initially it appears expensive, in the long run, it is a worthwhile investment. A galvanized structure lasts around 100 years.
The coating thickness depends upon the gauge of the metallic structure. The thickness of galvanization can be measured easily, whenever you wish. It is a non-destructive method…
Scientific process: Zinc oxide that acts as a protective layer occurs through a proven scientific process. It’s a natural metallurgical reaction.
Galvanizing is visible: Right from the beginning, galvanized steel structure starts showing its significance. Therefore, galvanizing is visible. It starts working from day one.
Complete coverage: Hot dip galvanizing helps in creating a very strong bond between zinc and steel. Thus it provides complete coverage, amazing strength, and durability. Owing to these features, the iron-made structures remain protected even during harsh weather conditions.
Summary
Hot dip galvanized steel is engulfing all of us in many different forms. It is all around us. Numerous companies, industries, sectors, etc. are leveraging the phenomenon, including automobiles, railways, power transmission, windmills, infrastructure, etc. Over the years, it has become integral to our lifestyle, and rightly so.
Buy the galvanization plant from Arvind Corrotech
Arvind Corrotech is an industry leader offering full-spectrum galvanization solutions. Our quality-driven product range includes Turnkey Hot Dip Galvanizing Plants, Pulse Fired High-Velocity Furnace, Process Tanks, Chemical Storage Tanks, and pollution control equipment.
If you are on the lookout for anything related to pollution control equipment, then end your search with Arvind Corrotech. Let’s connect for a mutually beneficial collaboration.