Tag: Galvanizing Furnace
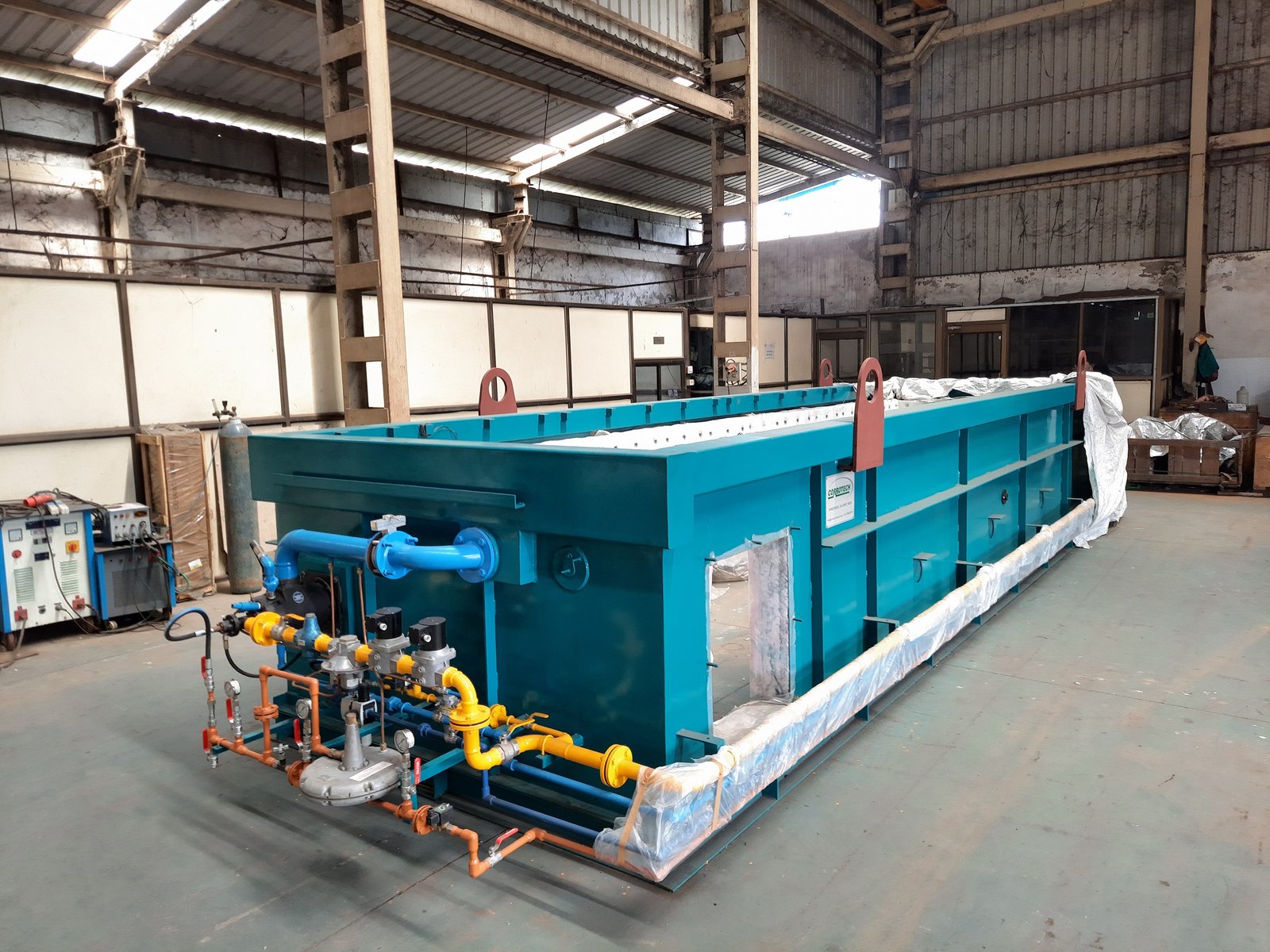
Scientists and socio-economic experts tracking the evolution of technology and innovation, and their impact on development have rightly called the invention of Galvanizing Furnace a milestone. The emergence of Galvanizing furnace has transformed the industry, especially the galvanizing sector.
So, what do you understand about the revolutionary product? What comes to your mind when you hear about product? Directly or indirectly, we all come across galvanized products. It could be a car, an auto rickshaw, an airplane, telecommunication and a wide range of construction material. However, we hardly ponder over the Galvanizing Furnace Process.
This blog makes a humble attempt to expand the knowledge of the readers about the landmark product.
Understanding the product
The Galvanizing Furnace is a sophisticated enclosure machine wherein the material is heated at a high temperature. A technology-driven temperature management system continuously keeps tabs on the temperature. The shelf life of this industry-centric product varies from company to company. Generally, it’s 20 years.
Whereas the requisite thermal energy is produced inside the combustion chambers during the galvanizing furnace process, the reason being, to keep the molten zinc according to the optimal temperature range. Heating intensity within the enclosure depends on the fuel being used. Fuels like gas, oil and electricity are being used. How to achieve excellence in a combustion chamber? That’s a moot question often raised by industry owners. Well, in this era of technology, flaws and excellence can be easily measured. Achieving excellence in combustion chamber remains the top priority of the industries. It’s the end result of accurate energy, balance calculation, construction engineering, quality of the enclosure and insulation material.
A kettle containing zinc gets heated through the Galvanizing Furnace. As far as the life of the kettle is concerned–it’s 7 – 9 years.
Industry experts recommend flawless fabrication technique to achieve brilliant quality hot dip galvanized coatings on fabricated article. Make sure that the fabricated assemblies, castings and other tools and technology for the Galvanizing Furnace Process conform to the local and global standards.
Heart matters
The industry experts weren’t exaggerating when they called the galvanizing furnace as the heart of a hot dip galvanizing plant. Engineering and design are important. Features like energy efficiency, durability and quality among others depend on design and engineering of the furnace. It doesn’t end here; even the profitability and performance of the furnace depend on engineering.
Ultimately, even the profitability of the plant is deeply connected to the quality of furnace engineering
Material used in manufacturing the kettle
The Galvanizing Kettle is manufactured using the special steel material with low carbon and silicon contents. The product has the strength to overcome the collision of zinc, and can endure high temperature.
Advantages of galvanization
Research has proved that galvanization is the best process to provide coating for metal and steel. A galvanized coating is unique in the sense that it’s an alloy of steel and matches features of steel.
Galvanization has been a blessing in disguise for the economic development. Here are a few advantages of galvanization:
- Lowest first cost
- Lowest long term cost
- Increases durability of the steel
- Reliability
- Robust coating
- Automatic protection for damaged areas
- Complete protection
- Entire surface can be coated within no time.
There are several types of coatings available to protect steel from corrosion. However, none of the coating matches benefits and properties of galvanization.
I’m confident, the blog will expand your knowledge base!
Leverage the unique expertise of Arvind Corrotech Ltd.
Arvind Corrotech is one of the leading companies offering Hot Dip Galvanizing Plants, Pulse Fired High Velocity furnaces, Pickling Tank, Flux Tank, Rinse Tank, Fume Extraction System, material handling systems and a wide range industrial storage tanks. The niche created through excellence enable the manufacturer with headquarter in Ahmadabad, India to cater to global companies.